SOLUTIONS
PARTAGER
LA DÉMARCHE TPM : PILIER DE L’ANALYSE DE LA PRODUCTIVITÉ
Considéré comme l’une des composantes du Lean Manufacturing, la Total Productive Maintenance (TPM) est une méthode visant à l’amélioration du fonctionnement des équipements d’une entreprise par l’optimisation de leur fiabilité et disponibilité. Par extension, on parle également de Total Productive Management pour sous-entendre une démarche globale de progrès impactant la stratégie organisationnelle de l’entreprise et sollicitant les différents services : production, qualité, maintenance et direction.
La mise en place d’une démarche TPM a pour objectif :
1- De rendre disponibles les KPI (indicateurs) indispensables au pilotage d’une démarche continue d’amélioration de la productivité,
2- De proposer des outils d’analyse synthétiques pour l’identification des sources de perte de performance.
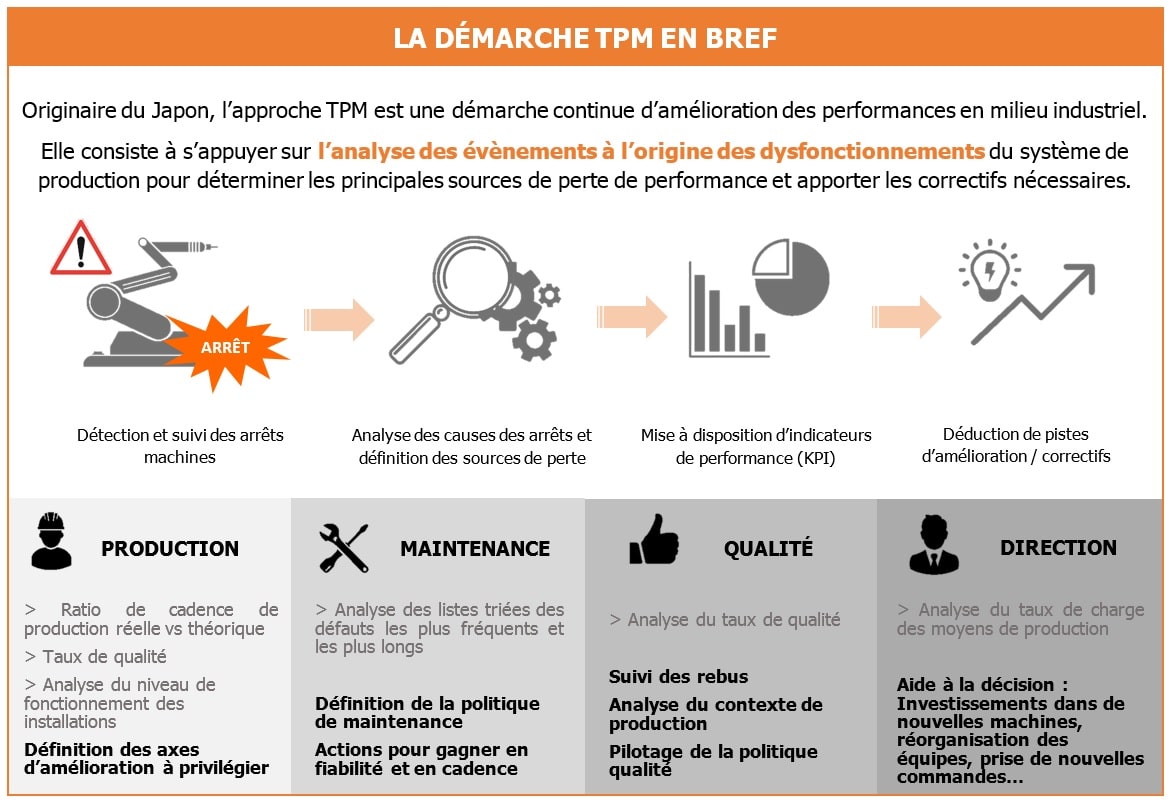
LA NORME NF E60-182 ET LES TEMPS D’ÉTAT DE PRODUCTION
Pour mesurer objectivement les performances de productivité selon une approche TPM, on peut différencier :
– les indicateurs usuels basés sur les rapports entre les différents temps de vie d’un équipement ou d’une installation (production/non production, qualité/non qualité),
– les indicateurs basés sur une classification et une analyse des différentes causes de perte de performance (exemple : pannes électriques, mécaniques, pneumatiques…, maintenance préventive, curative…).
La première catégorie d’indicateurs est définie par la norme NF E60-182 qui caractérise les différents « temps d’état » d’un équipement de la manière suivante :
– Le Temps d’Ouverture (TO) = le temps durant lequel l’accès à l’équipement est possible, c’est-à-dire lorsque l’installation n’est pas fermée.
– Le Temps Requis (TR) = le temps d’ouverture auquel on soustrait les arrêts planifiés tels que les opérations de maintenance, les pauses, les essais prévus sur l’équipement…
– Le Temps de Fonctionnement Brut (TFB) = le temps requis auquel on soustrait les arrêts propres tels que les pannes et divers problèmes non planifiés sur l’outil de production
– Le Temps de Fonctionnement Net (TFN) = le TFB auquel on soustrait les pertes de performance dues à des baisses de cadence, des problèmes opérateurs, des micros-arrêts et autres défauts machine
– Le Temps Utile (TU) : le TFN auquel on soustrait le temps passé à produire de la non qualité (rebus). Le Temps Utile correspond donc au temps effectif à produire de la qualité.
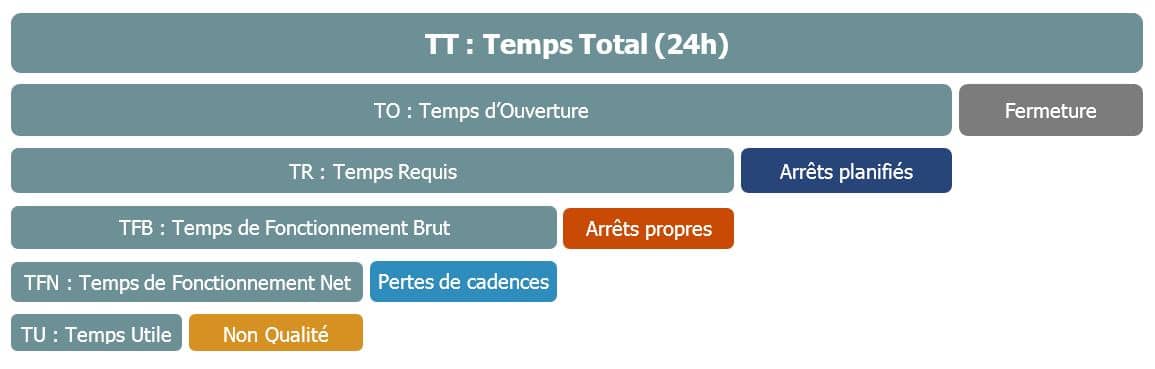
LE TRS, LE PLUS CONNU ET LE PLUS UTILISÉ
Très couramment pris en exemple dans l’industrie, le Taux de Rendement Synthétique correspond au temps durant lequel l’équipement est censé produire sans tenir compte des arrêts planifiés mais en intégrant tous les évènements non prévisibles et inhérents à une production automatisée : pannes, micro arrêts, pertes de cadence, non qualité, etc. Ce taux reflète donc le ratio de temps réellement utilisé pour produire de la qualité hors arrêts planifiés.
Taux de Rendements Synthétique (TRS) = Temps Utile (TU) / Temps Requis (TR)
Si le TRS est le taux le plus fréquemment utilisé, c’est parce qu’il permet une vision globale et immédiate de la performance de productivité sur un équipement. Il peut s’appliquer à tout type d’industrie, indépendamment du niveau de production, ce qui le rend universel. En revanche, il atteint rapidement ses limites s’il n’est pas mis en corrélation avec d’autres types d’indicateurs car il ne permet pas de définir la proportion de perte de productivité en fonction des sources de pertes de performance que peuvent être les problèmes de non qualité, les pannes, les pertes de cadence…
LE TRE ET LE TRG, AUSSI UTILES
Il existe d’autres indicateurs, moins fréquemment utilisés ou tout simplement oubliés, mais qui sont pourtant intéressants à prendre en compte pour une analyse pertinente de la productivité.
Le Taux de Rentabilité Economique (TRE) offre une visibilité sur la rentabilité de l’équipement ou de l’installation par rapport à son temps d’utilisation sur une période précise. Il s’agit du temps réellement consacré à produire de la qualité sur 24 heures.
Taux de Rendements Economique (TRE) = Temps Utile (TU) / Temps Total (TT)
Ce taux a son utilité car il délivre une information importante sur la capacité globale d’un équipement ou d’une installation à délivrer une production de qualité. Il permet à l’équipe dirigeante d’affiner la stratégie d’investissement de l’entreprise. Par exemple, il peut révéler la nécessité d’investir dans de nouvelles machines permettant d’augmenter le temps utile car plus performantes : moins de pannes, défauts machines, micro-arrêts…
Autre indicateur important, le Taux de Rendement Général (TRG) permet de mesurer le niveau de rendement d’un équipement par rapport au temps d’ouverture réel de l’atelier, en intégrant les arrêts planifiés comme les pauses, les entretiens de maintenance… Il s’agit donc du taux réellement utilisé pour produire de la qualité sur la période d’ouverture de l’atelier.
Taux de Rendements Général (TRG) = Temps Utile (TU) / Temps d’Ouverture (TO)
Comme il permet de mesurer la charge effective d’un moyen de production, il peut être révélateur en signifiant par exemple qu’il est nécessaire d’ajouter une équipe supplémentaire pour atteindre les objectifs de production attendus.
LES INDICATEURS RÉVÉLATEURS POUR LA MAINTENANCE ET LA QUALITÉ
On le voit au travers du découpage des temps de production défini par la norme NF E60-182, la performance des opérations de maintenance joue un grand rôle dans la productivité globale d’une entreprise. Pour mesurer cette performance, plusieurs indicateurs sont disponibles :
MTBF : Mean Time Between Failure = Temps Moyen entre pannes
Généralement exprimé en nombre d’heures, le MTBF est un bon indicateur pour déterminer si un équipement est fiable. Il peut évidemment être déterminant dans le choix de remplacement d’un équipement s’il est jugé trop court et entraîne des arrêts à répétition causant des pertes de performance de productivité conséquentes.
MTBF = Temps de Fonctionnement Brut / Nombre de Pannes
MTTR : Mean Time To Repear = Temps Moyen de Réparation
Le MTTR permet de mettre en évidence les temps de réparation sur un équipement pendant une période donnée. S’il s’avère trop long, il peut mettre en évidence la nécessité de trouver des solutions pour rendre les opérations de maintenance plus simples et plus rapides.
MTTR = Temps de Panne / Nombre de Pannes
DO : Disponibilité Opérationnelle
On peut dire d’un système de production qu’il est disponible lorsqu’il est en mesure de remplir la mission ou la fonction pour laquelle il a été conçu. Ce que l’on nomme la disponibilité opérationnelle d’un équipement correspond donc à son aptitude à la réparation par la mesure de l’efficacité de sa maintenance.
DO = MTBF / MTBF + MTTR
Taux de Qualité
Cet indicateur est évidemment fondamental pour piloter la politique qualité de l’entreprise. Il s’agit du rapport entre le nombre de pièces bonnes et le nombre de pièces produites. Plus le service qualité est rapidement informé de la chute du taux de qualité, plus il est capable d’intervenir dans les plus brefs délais pour apporter les actions correctrices. Les conséquences sur le maintien du niveau de productivité sont évidentes.
Taux de Qualité = Nbre de pièces conformes / Nbre total de pièces produites
Vous aurez saisi que l’application d’une démarche TPM (Total Productive Management) se traduit notamment par la mise à disposition de KPI révélateurs de l’activité de production. Ces derniers favorisent la prise de décision pour l’optimisation organisationnelle des services production et maintenance.
Pour aller plus loin dans l’analyse des pertes de productivité, une démarche TPM passe également par l’analyse des sources de perte de performance au travers d’une historisation et classification de l’ensemble des évènements (pannes, baisses de cadence, opérations de maintenance…). Cette analyse permet de disposer d’indicateurs et tableaux de bord complémentaires aux KPI usuels pour une réflexion approfondie sur les actions correctives à mener.
Pour aller plus loin
Une question, un projet ? Contactez-nous !
Contact