SOLUTIONS
PARTAGER
Le MES répond-il à toutes les situations ?
Dans le dernier article, nous apportions une première réponse à l’échange des données entre processus métier en faisant un point sur les logiciels dits MES (lire l’article). Mais quid des entreprises déjà équipées de logiciels, gérant ici l’ordonnancement, là la traçabilité ou encore la maintenance et qui ne peuvent s’offrir un MES complet ? ou bien qui sont équipées d’un MES ne recouvrant pas tous les processus métier ?
L’un des principaux freins à l’implémentation d’un MES, ou d’un nouveau MES, est la crainte de l’ampleur du projet et du budget à y consacrer (en centaines de milliers d’euros pour un MES complet) ou les ressources et le temps pour le déployer. L’autre frein important est sa capacité à remplacer des applications métiers déjà présentes dans les usines ou à coexister avec elles. En effet, beaucoup d’usines ont souvent déjà digitalisé, et ce depuis de nombreuses années, une partie des fonctions en adoptant des logiciels métiers comme une GMAO, une solution d’ordonnancement ou une gestion documentaire. Se pose alors la question de comment étendre la digitalisation à d’autres processus sans pour autant se séparer des outils logiciels préexistants.
Certaines entreprises peuvent également faire le choix de privilégier l’adoption de solutions logicielles spécialisées par service (maintenance, qualité, ordonnancement…) plutôt qu’un logiciel MES commun à l’ensemble de l’usine. Cela peut permettre d’adapter le niveau de digitalisation aux besoins réels de l’entreprise. Chaque service dispose alors de la solution logicielle qu’il juge la mieux appropriée aux réalités de ses usages.
L'interconnexion entre systèmes autonomes : pour une évolution progressive vers la digitalisation.
Le MES, selon l’ISA-95, est constitué de 11 fonctions, 11 briques fonctionnelles. Chaque processus métier de l’entreprise peut se digitaliser en déployant une brique logicielle hyper performante au moment où il est possible de le faire, en veillant à interconnecter l’ensemble des briques afin de constituer de façon agile un MES qui respecte la maturité, les ressources et les besoins d’évolution de l’entreprise.
Les entreprises qui font ce choix doivent alors veiller à privilégier des solutions logicielles ouvertes qui permettent le partage de données avec d’autres systèmes d’information. L’interopérabilité des solutions est réalisable soit par le déploiement de connecteurs natifs entre les différents systèmes, soit par la mise en œuvre de standards de communication industriels et informatiques. (lire notre article comment connecter deux logiciels en milieu industriel ?)
Les onze briques fonctionnelles du MES selon l’ISA-95 :
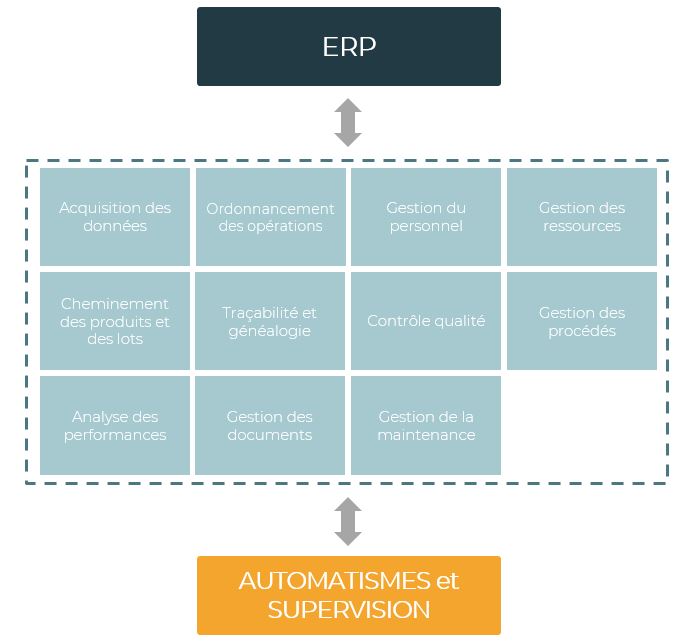
L’interopérabilité : faire interagir tous vos métiers pour démultiplier les gains.
Les exemples de données pertinentes pouvant être partagées entre les différents Systèmes d’Information sont nombreux. Prenons l’exemple des temps de marche d’un équipement. Ces données, collectées par les automatismes ou manuellement par les opérateurs, peuvent alimenter aussi bien une GMAO pour déclencher automatiquement des opérations de maintenance (à planifier en regard du planning de production) qu’alimenter le calcul automatique des rendements (TRS).
L’interconnexion des systèmes participe au décloisonnement de l’information dans l’entreprise en permettant à chacun de disposer des données adaptées à son niveau de décision. Elle permet de s’adapter aux moyens déjà en place et de construire par étape un échange des données de fabrication au sens du MES.
A retenir.
Que vous privilégiez une solution complète MES ou des solutions métiers autonomes, il est important d’impliquer les différents services concernés et de connaître les multiples flux de données amenés à circuler entre vos Systèmes d’Information industriels et vos systèmes de gestion et de décision. Choisir des solutions ouvertes qui facilitent l’interopérabilité avec d’autres systèmes d’information est primordiale pour garantir la pérennité de leur utilisation.
Pour aller plus loin
Une question, un projet ? Contactez-nous !
Contact