SOLUTIONS
PARTAGER
LES MOTIVATIONS DE LA TRANSFORMATION DIGITALE DU SUIVI DE FABRICATION
Devant la nécessité de répondre de manière immédiate, transparente et parfaitement adaptée aux attentes de leurs clients, les industriels doivent être en mesure de transformer leur chaîne de valeur pour plus d’agilité, de réactivité et d’innovation.
La digitalisation du suivi de la fabrication apparaît comme un moyen incontournable d’optimiser la performance industrielle pour maintenir leur compétitivité.
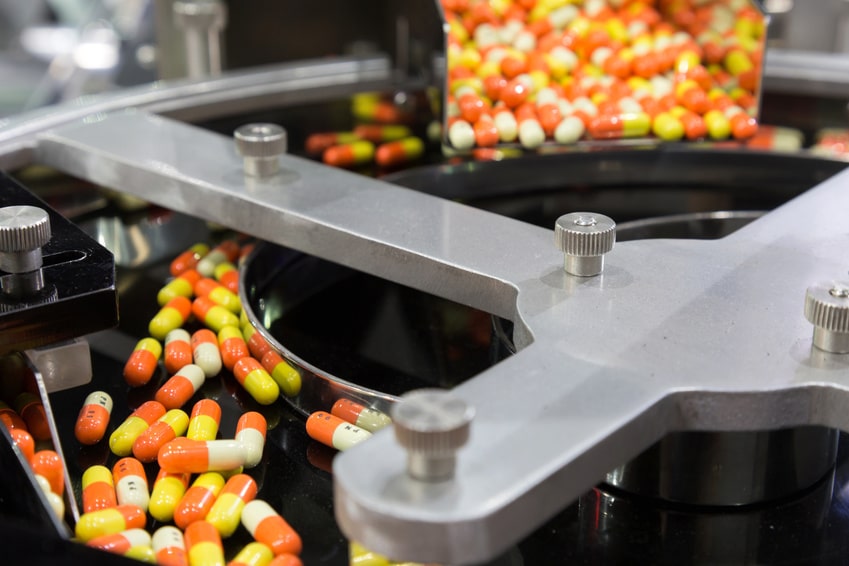
MAIS QUELLE SOLUTION LOGICIELLE RETENIR POUR RÉUSSIR SA DIGITALISATION ?
On distingue habituellement deux catégories de solutions pour la digitalisation des process de production dans l’industrie, communément appelées solutions MES pour « Manufacturing Execution System » :
– les solutions « généralistes »,
– les solutions « métier ».
LES SOLUTIONS « GÉNÉRALISTES » : LE TOUT-EN-UN ADAPTABLE
Elles rassemblent toutes les fonctions opérationnelles (production, maintenance, qualité…) au sein d’un seul outil qui présente à l’origine les mêmes caractéristiques fonctionnelles générales quel que soit le secteur d’activité de l’entreprise. Plutôt privilégiées par les grands groupes industriels, ces solutions présentent l’avantage de centraliser un large spectre de besoins fonctionnels de l’entreprise et de pouvoir bénéficier à grande échelle des avantages de la digitalisation. Elles peuvent s’adapter aux besoins particuliers des utilisateurs sous réserve de développements spécifiques.
LES SOLUTIONS « MÉTIER » : LE PRÊT-A-L’EMPLOI PARTIEL
Elles regroupent les fonctions opérationnelles de l’entreprise en tenant compte des spécificités métiers propres à un secteur d’activité précis (agroalimentaire, pharmaceutique, nucléaire…). Elles sont appréciées par les entreprises qui souhaitent disposer de solutions adaptées aux problématiques réglementaires ou fonctionnelles propres à leur secteur sans nécessiter de lourds développements spécifiques. Ainsi, un logiciel MES spécialisé pour le secteur pharmaceutique intégrera automatiquement les contrôles en cours de procédé (In-Process Controls) qui sont essentiels dans ce secteur hautement réglementé.
L’INTERACTION ENTRE SYSTÈMES AUTONOMES : L’ALTERNATIVE SUR-MESURE
Il existe néanmoins une troisième option visant à favoriser l’interaction entre les systèmes d’information « métier » autonomes. Ce modèle préconise le déploiement de connexions entre les différents systèmes d’information propres à chaque fonction de l’entreprise. En clair, le service maintenance dispose de sa propre solution adaptée à ses spécificités métier mais partage les données jugées pertinentes avec les autres systèmes d’information de l’entreprise.
L’interopérabilité des solutions est réalisable soit par le déploiement de connecteurs natifs entre les différents systèmes, soit par la mise en œuvre de standards de communication industriels et informatiques.
Cette solution présente l’avantage de s’adapter aux besoins fonctionnels réels dans l’entreprise en permettant à chaque service de disposer de la solution logicielle qu’il juge la mieux appropriée aux réalités de ses usages, tout en garantissant le partage de l’information entre services. Elle permet également d’affiner la maîtrise des coûts liés à la digitalisation en sélectionnant les interactions nécessaires au bon fonctionnement des échanges entre systèmes d’information.
EXEMPLES CONCRETS D’INTERACTIONS ENTRE SYSTÈMES
Prenons le cas des données concernant les temps de marche d’un équipement ou d’une machine. Ces informations, collectées à l’origine par le système de supervision ou manuellement par les opérateurs, peuvent alimenter le système de management des énergies (SME) qui en réalisera un traitement au travers de tableaux de bord et graphiques pour une analyse précise des consommations. Les données des temps de marche peuvent également être envoyées vers le système d’analyse des process (logiciel TPM : Total Productive Management). Le responsable de production disposera alors d’indicateurs fiables pour calculer ses taux de rendement. Quant à la fonction maintenance, elle utilisera les données de temps de marche pour déterminer automatiquement l’usure des pièces et planifier ses interventions.
En associant les données de plusieurs systèmes d’information « métier », l’ensemble des acteurs de l’entreprise disposent ainsi d’indicateurs fiables leur permettant :
– de prendre les décisions adaptées,
– d’identifier les pistes d’amélioration,
– de détecter les écarts et les dérives.
Pour aller plus loin
Une question, un projet ? Contactez-nous !
Contact