SOLUTIONS
PARTAGER
LA MÉTHODE TPM (TOTAL PRODUCTIVE MAINTENANCE)
Basée sur une démarche de progrès continu, la méthode TPM (Total Productive Maintenance) est considérée comme un outil d’analyse incontournable pour les personnels des services Production, Qualité et Maintenance. Elle a fait ses preuves en démontrant son efficacité dans l’amélioration de la stratégie organisationnelle et opérationnelle en milieu industriel. Son principe consiste à s’appuyer sur les évènements à l’origine des baisses de cadence et de la non qualité pour déterminer les principales sources de perte de performance et apporter les correctifs nécessaires.
Reste à savoir comment reconnaître les sources de perte de performance qui nuisent à la productivité dans votre entreprise et les utiliser pour en déduire les axes d’amélioration à apporter…
COLLECTER ET ENREGISTRER AUTOMATIQUEMENT OU MANUELLEMENT LES ÉVÈNEMENTS D’ARRÊT ET DE SOUS CHARGE.
Découvrir notre solution TPM
DécouvrirLa première étape dans la mise en place d’une démarche TPM consiste à détecter les évènements à l’origine des dysfonctionnements du système de production. Les causes conduisant à une perte de performance peuvent être multiples. Si certains articles sur le sujet évoquent souvent les « 6 grandes sources de perte de performance », d’autres praticiens de la TPM ont en réalité dénombré pas moins de 16 causes de perte, habituellement regroupées en 3 catégories (voir tableau ci-dessous).
Cette liste a le mérite de recenser la majorité des cas de perte de performance rencontrés en milieu industriel. Néanmoins, elle n’est pas exhaustive et il est possible que vous ayez vous-même identifié d’autres évènements causant des pertes de performance dans votre entreprise.
Dans tous les cas, la multiplicité des facteurs pouvant conduire à une baisse de productivité et la récurrence potentielle de certains d’entre eux dans votre quotidien rendent très difficile leur recensement et par conséquent leur analyse a posteriori si l’on ne dispose pas de solution logicielle adaptée.
⇒ Choisir un logiciel capable d’enregistrer de manière automatique et manuelle les événements sources de dysfonctionnement est capital pour engager une démarche TPM efficace.
Si vous disposez d’un système de production automatisé, le logiciel devra être en mesure de se connecter directement aux automatismes pour utiliser les données relevant d’un arrêt ou d’un ralentissement du système de production. Il devra également permettre la saisie en direct par un opérateur dans le cas de process non automatisé.
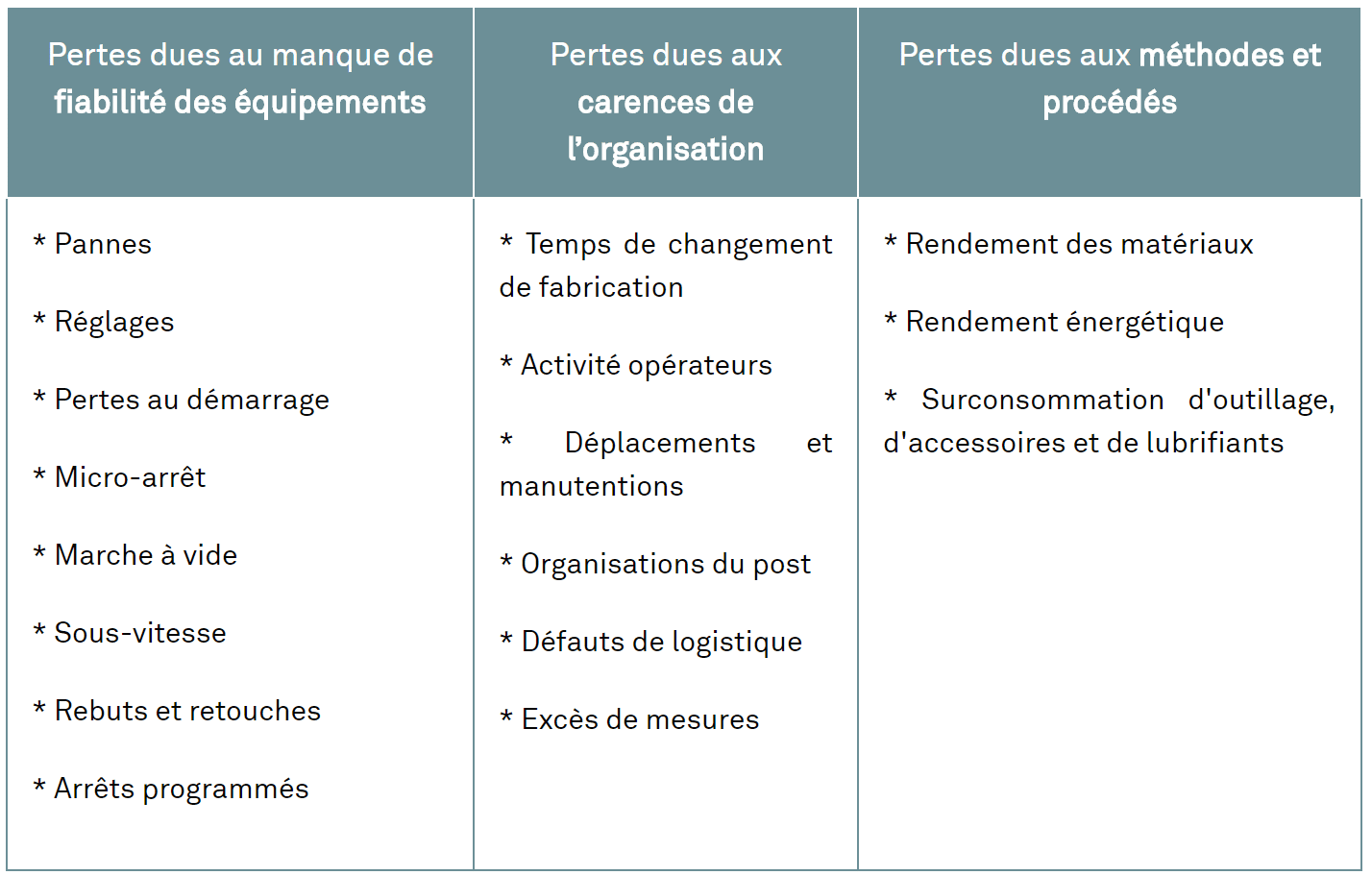
PROCÉDER À UNE CLASSIFICATION PERSONNALISÉE ET AUTOMATISÉE DES SOURCES DE PERTE.
Une fois que les données relevant des dysfonctionnements ont été collectées, il est nécessaire de pouvoir mesurer la durée et la fréquence des événements puis de les classifier pour en effectuer une analyse postérieure.
La mesure de la durée et de la fréquence des événements est essentielle pour cibler les actions prioritaires à mener pour améliorer la productivité. Quant à la classification, elle consiste à attribuer chaque événement à une famille de causes communes à d’autres événements. C’est une étape nécessaire pour obtenir une analyse macro des sources de perte. Elle doit être propre à votre organisme, c’est-à-dire que vous devez pouvoir définir si un événement relève dans votre entreprise d’un défaut organisationnel, de maintenance, d’approvisionnement, de qualité… Seule une hiérarchisation personnalisée des événements vous permettra de disposer d’une approche analytique structurante (voir exemple ci-dessous).
⇒ Disposer d’un logiciel classant automatiquement les événements par durée/fréquence et les regroupant par causes selon vos propres modèles facilite l’analyse de vos baisses de productivité.
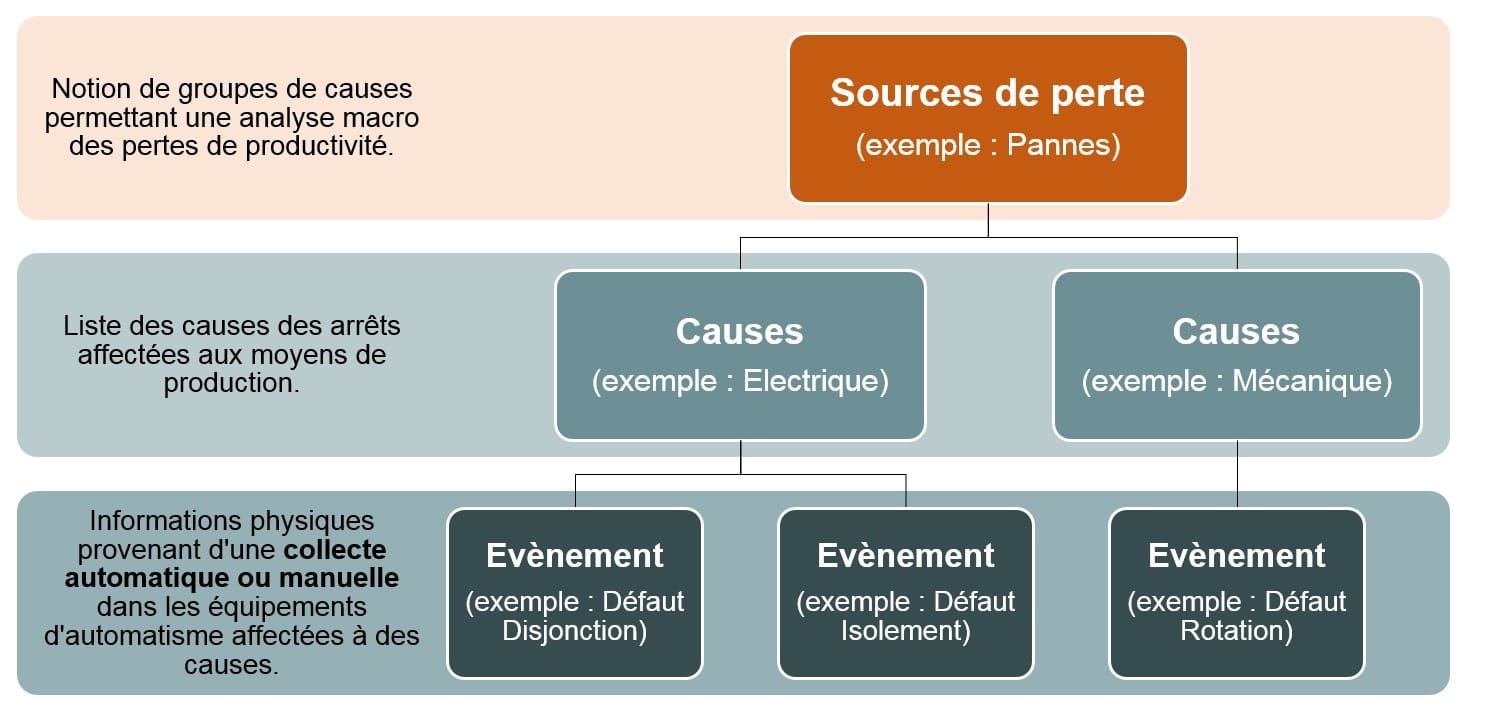
ADAPTER L’ANALYSE DES SOURCES DE PERTE DE PERFORMANCE SELON LES MÉTIERS ET OBJECTIFS.
Pour déduire les pistes d’amélioration pertinentes, il faut pouvoir accéder à un ensemble de rapports et tableaux de bord permettant une analyse rapide des sources de perte de performance en fonction des types d’équipement, des lots de fabrication, des temps de production…
⇒ Vous devez pouvoir créer à tout moment autant de rapports dynamiques et d’interprétations graphiques que vous jugez nécessaires pour une analyse pertinente de vos sources de perte de performance.
L’analyse TPM est potentiellement utile à de nombreux acteurs dans l’entreprise issus de services différents : Maintenance, Production, Qualité, voire Direction. Chacun doit pouvoir utiliser les données qui lui sont utiles pour apporter sa contribution à l’amélioration globale de la productivité dans l’entreprise. Il faut donc une solution offrant une liberté et une facilité de paramétrage pour une présentation des données adaptée à chaque profil.
DISPOSER D’UNE ANALYSE TPM PAR PROFIL, POUR QUI ET POURQUOI EST-CE UTILE ?
- L’Opérateur : cela lui permet de connaître en quasi temps réel la cadence de production réelle par rapport à la cadence théorique prévue.
- Le Responsable de Production : il va pouvoir analyser le fonctionnement des installations et dégager ainsi les axes d’amélioration concernant l’organisation de la production et la qualité des matières produites.
- La Maintenance : l’analyse des listes triées des défauts (les plus fréquents, les plus longs) va permettre de définir et d’ajuster la politique de maintenance. En ciblant les actions sur les points techniques importants, des gains en termes de fiabilité et de cadence pourront être dégagés.
- La Direction : Grâce à l’analyse des taux de charge des moyens de production, elle pourra mieux orienter la politique d’investissement dans les nouveaux équipements et améliorer l’organisation des équipes.
Pour aller plus loin
Une question, un projet ? Contactez-nous !
Contact